Crane coatings are an essential part of the overall crane construction. They serve multiple purposes, including protecting the crane from corrosion and wear and tear, improving its visibility, and enhancing its appearance. Coatings also help to increase the lifespan of the crane, making it more durable and reliable.
To ensure that crane coatings provide optimal protection and longevity, various coating thickness requirements must be met. These requirements are dependent on several factors, including the type of coating used, the crane's location, and its application.
One of the most critical requirements for crane coatings is a specific thickness. The thickness required may vary depending on the type of coating and the environmental conditions to which the crane is expected to be exposed. In general, a minimum thickness of 80 microns is recommended for the crane's primary components, such as the jib, or boom. However, this thickness may increase to 200 microns or more for cranes working in extreme conditions.
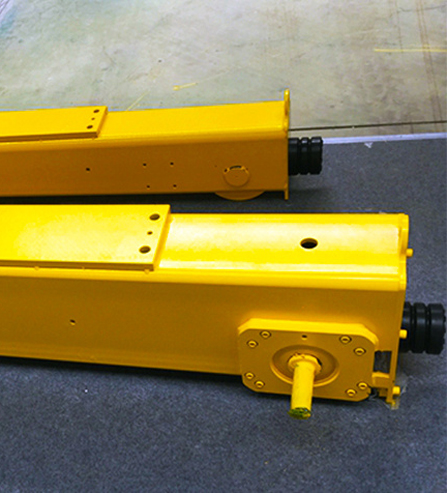
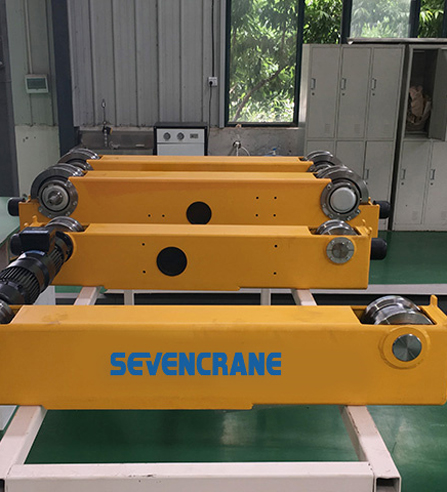
Another essential aspect of crane coating thickness is consistency. The coating should be evenly applied across the entire surface, ensuring that no areas are exposed to the elements. This is especially important for cranes working in harsh environments, such as saltwater areas, where corrosion can quickly take hold.
It is also crucial that the coating material used is suited to the crane's application. For example, a crane operating in a chemical plant should have a coating that is resistant to chemical corrosion, while a crane working on an offshore oil rig may require a coating that can withstand saltwater corrosion.
Overall, meeting crane coating thickness requirements is critical to the crane's longevity and performance. A well-applied and consistent coating can provide adequate protection to the crane in even the most challenging conditions. A properly coated crane will be more reliable, efficient, and less prone to breakdowns.
Post time: Oct-10-2023