1. Electrical Failures
Wiring Issues: Loose, frayed, or damaged wiring can cause intermittent operation or complete failure of the crane’s electrical systems. Regular inspections can help identify and fix these issues.
Control System Malfunctions: Problems with the control panel, such as unresponsive buttons or faulty circuit boards, can disrupt crane operation. Calibration and testing can prevent these faults.
2. Mechanical Problems
Hoist Issues: The hoist mechanism can experience wear and tear, leading to problems like uneven lifting, jerky movements, or complete hoist failure. Regular lubrication and inspection of hoist components can mitigate these issues.
Trolley Malfunctions: Issues with the trolley, such as misalignment or wheel damage, can hinder the crane's movement along the runway. Proper alignment and maintenance of trolley wheels and tracks are essential.
3. Structural Failures
Runway Beam Misalignment: Misalignment of the runway beams can cause uneven movement and excessive wear on the crane’s components. Regular alignment checks and adjustments are crucial.
Frame Cracks: Cracks in the crane’s frame or structural components can compromise safety. Routine structural inspections can help detect and address such issues early.
4. Load Handling Issues
Slipping Loads: Inadequate securing of loads can lead to slipping, causing potential safety hazards. Ensuring proper rigging and using appropriate lifting devices are vital.
Hook Damage: Damaged or worn hooks can fail to secure loads properly, leading to accidents. Regular inspection and replacement of worn hooks are necessary.
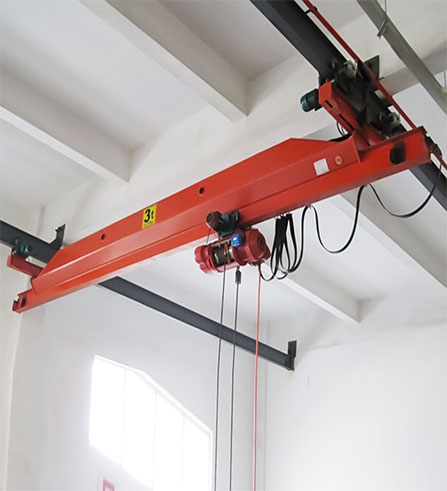
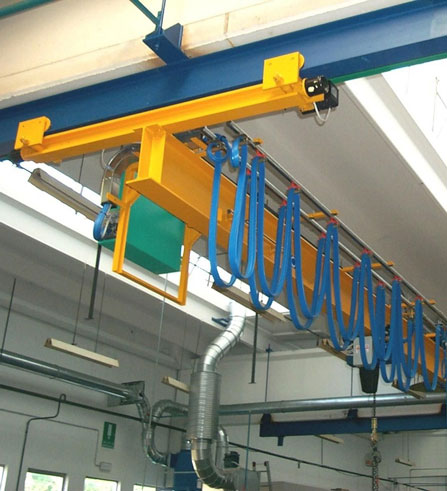
5. Brake Failures
Worn Brakes: Brakes can wear out over time, reducing their effectiveness and leading to uncontrolled movements. Regular testing and replacement of brake pads and components are important.
Brake Adjustment: Improperly adjusted brakes can cause jerky stops or inadequate stopping power. Regular adjustments and maintenance ensure smooth and safe operation.
6. Overloading
Overload Protection: Failure of overload protection devices can lead to lifting loads beyond the crane’s capacity, causing mechanical strain and potential structural damage. Regular testing of overload protection systems is essential.
7. Environmental Factors
Corrosion: Exposure to harsh environments can cause corrosion of metal components, affecting the crane’s structural integrity and performance. Protective coatings and regular inspections can help mitigate corrosion.
8. Operator Errors
Inadequate Training: Lack of proper training for operators can lead to misuse and increased wear on the crane. Regular training and refresher courses for operators are crucial for safe and efficient crane operation.
By addressing these common faults through regular maintenance, inspections, and operator training, the reliability and safety of underslung overhead cranes can be significantly improved.
Post time: Aug-09-2024